Проблемы и последствия подделки подшипников качения
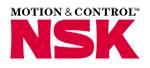
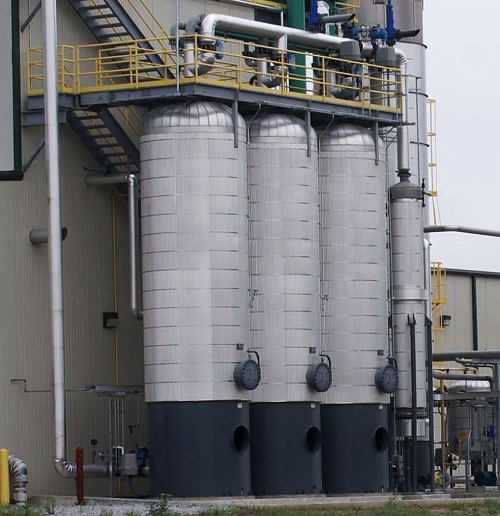
Использование сепарирующей центрифуги для экономии места в промышленном процессе дистилляции
Фундаментальное понятие процесса дистилляции подразумевает, что разделение фракций жидкой смеси может происходить не только при нагреве, но и при вращении центрифуги. В проводимом исследовании акцент был сделан на сепарирующей центрифуге, в которой критическим является радиус барабана, а не его высота, чтобы в полной мере использовать в процессе возникающие центробежные силы. Преимущество этих устройств заключается не только в меньшем пространстве для установки, но и процесс дистилляции в них протекает более интенсивно из-за более эффективного разделения фракций смеси при вращении.
Продолжительность процесса в сепарирующей центрифуге существенно меньше по сравнению с использованием нагревательных колонок. Кроме того, процесс и его результаты разделения непосредственно зависят от турбулентности и скорости вращения барабана, которые могут быть быстро изменены. Другое преимущество сепарирующих центрифуг заключается в быстром запуске процесса. Поэтому центрифуга очень хорошо подходит для циклических процессов: как только жидкость будет собрана в контейнере в определенном количестве, сразу же запускается процесс дистилляции.
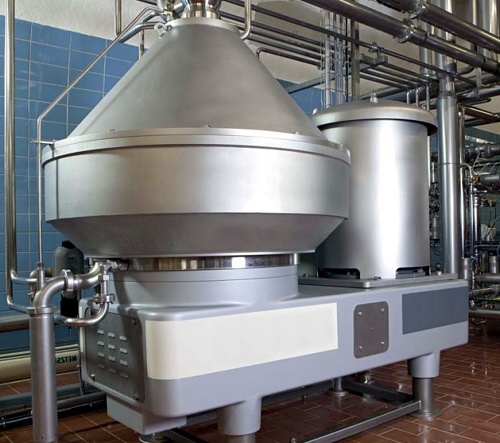
Для продвижения проекта было достигнуто согласие по строительству опытного завода китайскими партнерами. Проект состоял из трех этапов, и на первом этапе была запланирована установка модульной системы сепарирующей центрифуги с диаметром барабана приблизительно 90 см.
Проектирование опытного завода было завершено в начале 2011 г. и затем началось его строительство. В феврале 2012 г. завод в Китае был принят в эксплуатацию. В ноябре 2012 г. система дистилляции была настроена в Дортмунде - первоначально без периферийного оборудования. При первых испытаниях системы сразу же возникли проблемы: приблизительно после 20 минут работы произошел ясно слышимый удар в силовом приводе, даже при том, что он вращался только в половину проектной скорости вращения.
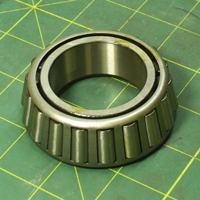
Наконец, инженеры извлекли подшипники качения и попытались связаться с их производителем - компанией NSK. После осмотра подшипников все предположили, что причина кроется в ошибке конструкции, а точнее, в отсутствии зазора в коническом роликовом подшипнике. На основании такого заключения была проведена регулировка этих подшипников и выставлен больший зазор в подшипнике. Но после того, как привод был собран повторно и проведено его испытание, оказалось, что никакого существенного изменения в работе установки не произошло.
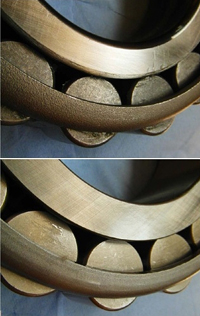
После того, как специалисты NSK получили детализированные изображения подшипников, всем стало ясно: все подшипники были подделкой и не являлись изделиями производства NSK. Изготовители фальшивок предприняли большие усилия, чтобы придать подшипникам внешнее сходство с оригинальными изделиями - даже логотип компании выглядел обманчиво подлинным. Лучшим способом для определения различия между оригиналом и подделкой стало качество обработки отдельных компонентов подшипника.
Оригинальные высококачественные подшипники исключили какое-либо повышение рабочей температуры
Новые подшипники были заказаны у одного из авторизованных дистрибьюторов NSK и затем установлены. Пробные испытания продемонстрировали, что температура подшипников и вала оставалась ниже температуры окружающей среды, даже после девяти часов непрерывной работы, потому что оригинальные подшипники имели значительно более высокое качество изготовления и в материале и в механической обработке. Теперь охлаждение привода могло функционировать должным образом, и исчезли посторонние звуки. Кроме того, привод вращался более гладко и тише, чем прежде.
В итоге было определено, что использование поддельных подшипников привело к задержкам запуска в эксплуатацию установки и в исследовании нового процесса дистилляции. Инженеры всегда должны помнить, что при использовании поддельных подшипников в областях применения, связанных с безопасностью производства, отрицательные результаты могут быть намного более серьезными. Если потребители не желают оказаться в сложной ситуации, то им следует обратить внимание на систему поставок, и заказывать изделия из надежных источников, то есть у авторизованных партнеров по дистрибуции производителя подшипников качения.
Приведенный выше пример показывает, что попытки производителей подшипников исследовать поддельный продукт приносят одинаковую пользу и заказчикам и эксплуатирующим организациям. Компания NSK, следуя своей политике, присоединилась к Международной ассоциации производителей подшипников (WBA) и поддерживает потребителей своей продукции в идентификации подшипников качения в целях защиты их от подделок.
Источник информации: www.nskeurope.com